7 Most common mistakes in soldering? (Solutions, 2023)
Soldering can be a straightforward process, several mistakes can be done by a beginner. These errors can lead to unreliable connections, damaged components, and frustration.
The most common mistakes in soldering are, poor temperature control, moving the joints too soon, no use of flux, rushing the process, improper use of solder, poor wetting, poor tip maintenance, and lack of practice. Proper handling of the soldering process and soldering iron temperature can help you to avoid these mistakes.
In the rest of this article, we’ll look at some of the most common soldering mistakes and how to avoid them.
What are the most common mistakes in soldering?
As we know soldering is the process to join metal with heating so happening of mistakes is a must at the beginner level. Maybe you don’t provide proper heat or disturbed the joint soon can affect the soldering joints.
Doing mistakes is part of learning even experienced hobbyists often fall victim to some common mistakes that can lead to faulty connections, damaged components, and wasted materials so don’t worry.
Let’s discuss the soldering mistakes and how can we correct them.
1. Poor temperature control
One of the primary mistakes during soldering is poor temperature control. Enough temperature should be provided to solder to melt down and create strong electrical connections.
If the proper temperature is not provided or the soldering iron is not hot enough, the solder won’t properly melt, leading to what’s known as a “cold joint”.
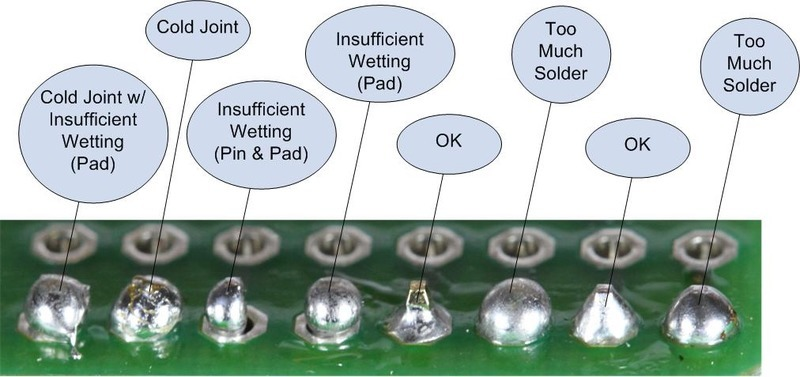
Cold joints are weak and unreliable connections that can break and can lead to the overall failure of the system.
On the flip side, applying too much heat can also cause problems. Overheating components can lead to damage, such as the burning of components or circuit boards, and the melting of insulation on wires.
Excessive temperature can also degrade the overall quality of solder joints and make the connection less reliable in the long run.
Proper temperature control is very important, use adjustable temperature settings and practice controlling temperature to prevent excess or insufficient heat problems.
2. Moving the joint too soon
Another mistake that can happen during soldering is moving the joint too soon, which means when you apply solder to the joint you don’t wait for it to solidify completely.
Moving or disturbing the joint while the solder is still molten can result in what’s known as a “dry joint,” where the solder doesn’t properly bond with the surfaces. This will lead to weak soldering joints or failure with time.
Give some time for to solder to cool down naturally and if you want to move components move them gently.
3. No use of flux
Flux is an essential compound used during the soldering process. It helps clean the surfaces being soldered, prevents oxidation during heating, and promotes good solder flow. Some beginners don’t know about the flux or some neglect it assuming it is unnecessary.
Flux act as a cleaning agent and aids in cleaning the surfaces to ensure a successful solder joint.
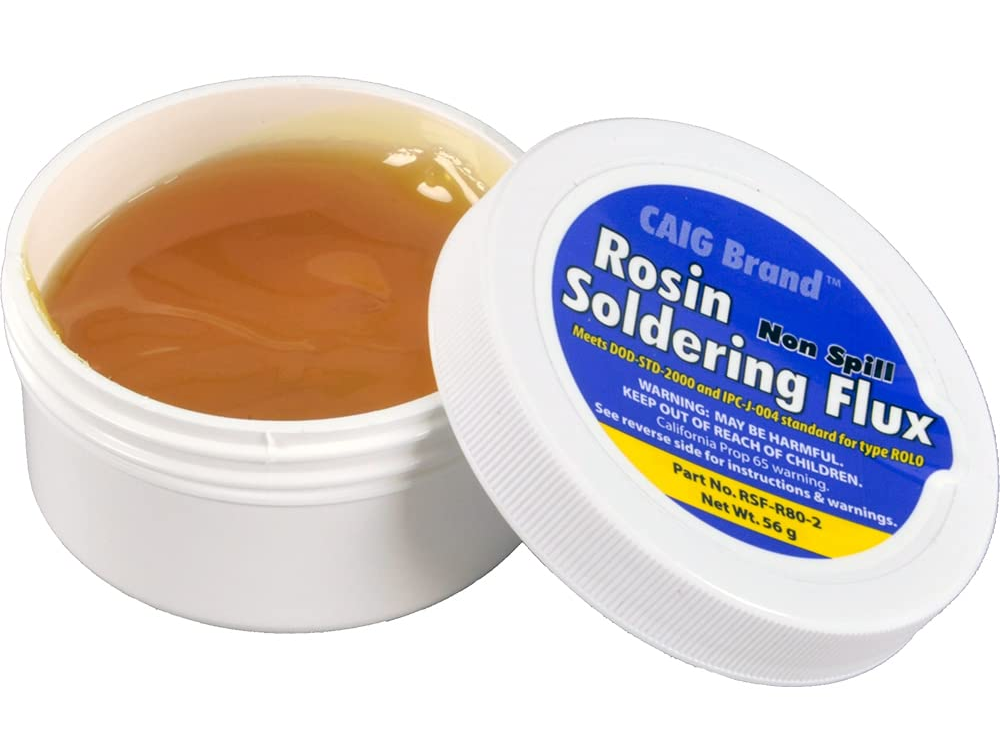
Skipping the flux during soldering can result in weak joints, higher chances of cold joints, and difficulties in achieving proper solder flow. Make sure you use flux that is compatible with your project components to ensure strong solder joints.
4. Rushing the process
Soldering requires lots of patience and precision. If you start rushing the soldering process there is a high risk that you will do mistakes. This will lead to unreliable soldering connections.
Take your time and placed the components correctly, heat the joints to their accurate temperature and allow the solder to flow evenly to make an excellent soldering connection. Avoid moving the pieces before the solder has solidified, as this can result in cold joints.
5. Improper use of solder
The uneven flow of solder or applying too much and too less solder is also a common mistake that can happen.
Applying too much solder can lead to solder bridges or short circuits between adjacent connections. It can also create bulky and unsightly joints that may interfere with the proper functioning of the circuit.
On the other hand, applying too less solder will make the joint starved for solder. It will create a weak connection which may fail with time. Remember to apply the right amount of solder during soldering to create clean and efficient connections.
6. Poor wetting
Wetting is the ability of solder to flow evenly onto the surfaces being joints. To have clean and shiny joints the wetting property of solder is crucial.
Various factors can cause poor wetting such as dirt, grease, or oxidation on the surfaces.
To avoid poor wetting, make sure you clean the surface thoroughly before the soldering process using an appropriate cleaning agent. Additionally, using flux like this one (Amazon link) can help improve wetting by promoting better solder flow and reducing surface tension.
7. Poor tip maintenance
With frequent use or maybe after one use the tip of the soldering iron oxidized, accumulating dirt and solder residue. This affects the heat transfer property of iron’s tip to the joints and results in cold, weak, and unreliable soldering connections.
You have to take care of the tip by properly maintaining it. Different cleaning methods are used to clean the tip of iron such as cleaning with a wet sponge or brass sponge when the dirt and oxidation are mild.
For excess oxidation, you can also use sandpaper but sandpaper needs a proper handle as it is an abrasive material it can damage the tip if mishandled. While soldering do not avoid the cleaning of a tip as it has a lot of negative affect on soldering iron performance.
8. Lack of practice
Soldering is an art and it needs a lot of practice to be an expert in it. The lack of practice also leads to a lot of mistakes in the soldering process.
Try to practice on less complicated projects to improve your soldering skills and gradually move towards more complex and difficult projects or tasks. Use different soldering techniques to get familiar with it and that will help you in the future.
Practice will reduce the chances of mistakes and will help you to learn more and produce more.
Conclusion
Soldering is a valuable skill for anyone working with electronics or engaging in DIY projects. It is a process that helps to give life to our ideas. By understanding the common soldering mistakes and steps on how to avoid them you can ensure reliable soldering connections.
Having a good understanding and control of temperature, giving time to the joint to cool down, and making use of good soldering flux you will have a smooth soldering journey and strong connections.
Make sure you use the right amount of solder while creating connections, keep the tip of a soldering iron and maintain it and practice different soldering techniques to avoid mistakes. Additionally, soldering is not a process where you can be shown impatience, be patient and enjoy your soldering work.
Remember, with practice and attention to detail, you’ll be able to master the art of soldering and confidently tackle various projects.
Other useful posts: